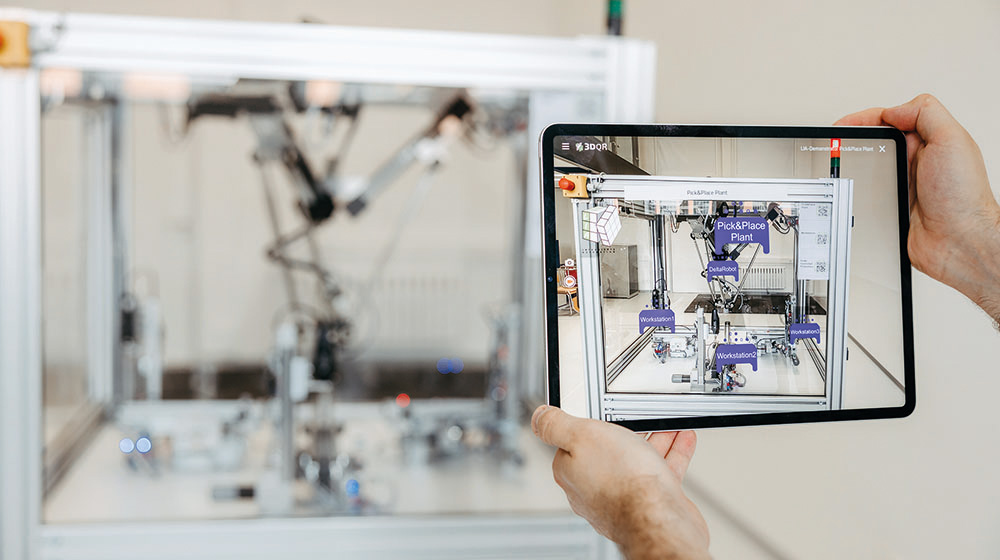
Once the Babylonian people wanted to build a tower high in the sky to stand eye-to-eye with God. But God created a confusion of languages to thwart this project. Difficulties in communication did not allow the project to come to a happy end. Since then, people with different languages have lived scattered all over the world - as the story of the Tower of Babel tells us. The "Babylonian tangle of languages" has survived as a saying to this day. People - because they are intelligent - have found ways to communicate around the world; despite their language barriers.
In their unbridled thirst for research, they have long wanted to teach their machines to communicate and work intelligently with each other. The digital age is opening up completely new possibilities. However, a "Babylonian confusion of languages" would also lead to problems here. "It stands to reason that a precise and unambiguous language is important for machines to communicate with each other," says Christian Diedrich, head of the Integrated Automation Department at the Faculty of Electrical Engineering and Information Technology at Otto von Guericke University Magdeburg. The university shares its vision of smart value chains with the German Engineering Federation and the Electrical and Digital Industry Association. Together with companies from mechanical engineering, the electrical industry and the software sector, Christian Diedrich's group is working in the "Industrial Digital Twin Association," which was founded in 2021.
Prof. Dr.-Ing. Christian Diedrich (Photo: Jana Dünnhaupt / Uni Magdeburg)
"The communication of components and entire industrial plants is to be conducted via their digital twins," says Christian Diedrich. He heads the Industrial Digital Twin project at Magdeburg University. Its core task is to enable interoperability, i.e. cooperation between different digital twins, worldwide. "We participate in the development of technical norms, of common standards to which IT systems must adhere," says the professor of integrated automation. Diedrich praises mechanical engineering performance "made in Germany": "Machines from Germany still have a very good reputation on the world market." Mechanical engineering, with its rich tradition, is still the largest discipline at University of Magdeburg.
The technical monument of a steam engine on the university campus is a reminder of the first industrial revolution. Via the introduction of electricity (2.0) and the use of electronics and IT (3.0), the transformation of industry is now leading to Industrial Revolution 4.0 - characterized by intelligent, self-organizing plants and machines. The University of Magdeburg has also earned an excellent reputation in these specialist areas. "If our machines are to be components of intelligent, autonomous, self-organizing value chains in the future, then we have to put them in this technological performance state. And we can do it," the expert is convinced. This is because automation technology combines the mechanical engineering, electrical engineering and information technology competencies at University of Magdeburg.
The processing stations are supplied with orders by means of I4.0 language (Photo: Jana Dünnhaupt / Uni Magdeburg)
The University of Magdeburg is one of the representatives from business, science and politics who have joined forces on the Industrie 4.0 platform to advance the digital transformation of production in Germany and strengthen the competitiveness of the manufacturing location. Working groups aim to answer important questions about the future - including system architecture, models and standards. "We are developing the foundations for open standards that are valid for both the user and supplier industries for hardware and software," says Christian Diedrich. Clearly, the aforementioned Babylonian confusion of languages would not be manageable even by intelligent machines. Especially within a value-added process, it is important that information is understood accurately and in real time.
Christian Diedrich and his research associates Chris Urban, Alexander Belyaev and Harish Pakala are using a demonstrator for smart order-driven production to show how the physical and virtual worlds are merging. Here, developers throughout Germany have the opportunity to connect their digital twins à la the Industrie 4.0 platform, also known as the administrative shell, and test how they network with each other - from automated order planning and order placement to autonomous production control. If an error occurred in this process, the management shells would independently search for alternatives so that production would not have to be halted. The miniature system, which produces a cylinder completely autonomously from a metal blank, has already attracted a great deal of attention at trade shows and congresses.
Alexander Belyaev operates the system via an AR app (Photo: Jana Dünnhaupt / Uni Magdeburg)
Chris Urban scans QR codes that mark each of the real parts of the plant: the assets. "Behind each QR code is a virtual image of the real part, a digital twin," Urban explains. He studied mechatronics and is involved in the development and optimization of this Germany-wide demonstrator. According to his explanations, the management shells can actually be thought of as storage boxes that receive a lot of important information about the real existing machine part in each case and then manage it. The digital twin of the "cylinder" product, for example, knows the production steps and the requirements associated with this production process. Completely autonomously, it initiates the necessary machining processes such as drilling and grinding because it can communicate with the digital twins of the tools required for this purpose. "Each message element has an identification number and is thus understandable to the machines," says Alexander Belyaev. He studied electrical engineering and information technology at Magdeburg University and is researching the semantics of digital twins; that is, the linguistic signs that have, or should have, a uniform meaning throughout the world. "We are developing the concept for a digital lexicon in which it is possible to see what the IDs mean, arranged under subject areas," says Belyaev.
Chris Urban shows details of the I4.0 language in the interaction between machines (Photo: Jana Dünnhaupt / Uni Magdeburg)
Meanwhile, Chris Urban's tablet documents how the digital twins responsible for the "drilling" work process communicated and made their decisions without any central controlling authority. Essential to this communication is the networking of the digital twins in the "Internet of Things," where they exchange data, for example, about the capabilities, properties and states of the real components; for example, about the material properties of the blank from which a cylinder is to be made and about the requirements that are placed on the product. But the log also shows what else the management shells can "manage". They search across company boundaries for machines and production sites that can manufacture the product according to defined parameters within a certain time and price range. They integrate capabilities and free capacities of other companies into their own production and thus expand their own spectrum. At the same time, they examine possibilities of offering their own free production capacities on the market in order to achieve a higher utilization of the machines. The aim of such intelligent process chains is to make production more efficient and conserve resources. The term "Industry 4.0 ecosystem" is new in this context.
Harish Pakala shows the digital twin he developed (Photo: Jana Dünnhaupt / Uni Magdeburg)
To ensure that research and development within the Industrial Digital Twin project does not miss the needs of users, the university maintains close cooperation with partners from industry, such as the machine and plant manufacturer Wittenstein or the SmartFactory technology initiative, and with partners from research, such as the Rheinisch-Westfälische Technische Hochschule Aachen, the Fraunhofer Institute for Industrial Automation IOSB-INA Lemgo and ifak - Institute for Automation and Communication Magdeburg. For all of them, a very obvious question arises: Where should all this information be processed? Project manager Diedrich points to a real-practice example of understanding and cooperation between automation and IT experts, from which a genuine innovation emerges: "Data processing is to be integrated directly into the plants as far as possible. This solution even reduces the CO2 footprint of these intelligent machines."
GUERICKE facts
- A "digital twin" is a data and software image of machines and plants. It provides information about construction, commissioning, operational use, and even scrapping.
- Clouds, the Internet of Things or blockchain can be used to network machines, plants and entire smart factories. For this, all data must be machine-readable and machines must be able to understand each other using a unique language.
- The I40 language defines rules for vocabulary, sentences and dialogs analogous to a human language.